دستگاه تیوب پرکن تمام اتومات لمینیت یکی از تجهیزات پیشرفته و ضروری در خطوط تولید محصولات آرایشی، بهداشتی، دارویی و شیمیایی است. این دستگاه مخصوص پر کردن و سیل کردن تیوبهای لمینیتی طراحی شده و قابلیت انجام تمام مراحل بهصورت خودکار را دارد؛ از پر کردن دقیق تا درزگیری حرارتی، چاپ تاریخ، برش و خروج منظم محصول.
تیوبهای لمینیت به دلیل ظاهر حرفهای، مقاومت بالا در برابر نفوذ هوا و قابلیت چاپ عالی، امروزه بسیار پرکاربرد هستند. بنابراین استفاده از دستگاهی که بتواند این تیوبها را با کیفیت و سرعت بالا پر کند، در تولید صنعتی بسیار اهمیت دارد.
تیوب پرکن تمام اتومات لمینیت ارکان فلز با عملکرد دقیق و قابل تنظیم، باعث افزایش بهرهوری و کاهش خطای انسانی در خط تولید میشود. این دستگاه به کمک سیستم PLC و پنل لمسی، امکان کنترل کامل فرآیند را برای اپراتور فراهم میکند.
در سایت ارکان فلز میتوانید مشخصات فنی این دستگاه، ویدیوهای آموزشی، مشاوره خرید و قیمت بهروز را مشاهده کنید. اگر بهدنبال ارتقاء کیفیت بستهبندی محصولات خود هستید، این دستگاه انتخابی ایدهآل برای شماست.
تیوب پرکن چیست و چه کاربردی دارد؟
تیوب پرکن دستگاهی تخصصی در صنایع بستهبندی است که برای پر کردن تیوبها با مواد نیمهمایع یا غلیظ مانند کرمها، ژلها، خمیر دندان، پمادهای دارویی و انواع محصولات آرایشی به کار میرود. این دستگاهها در مدلهای مختلفی مانند دستی، نیمهاتومات و تماماتومات تولید میشوند و بسته به نیاز خطوط تولید، میتوان از آنها در مقیاسهای کوچک تا صنعتی استفاده کرد.
تیوب پرکنهای تماماتومات با توانایی بالا در پر کردن، درزگیری، کدگذاری، برش و بستهبندی تیوب، نقش مهمی در افزایش بهرهوری خطوط تولید دارند. این دستگاهها قابلیت کار با انواع تیوب مانند پلاستیکی، آلومینیومی و لمینیتی را دارند و دقت بالای آنها باعث کاهش ضایعات و افزایش کیفیت نهایی محصول میشود.
در سایت ارکان فلز شما میتوانید مشخصات فنی انواع تیوب پرکن را بررسی کرده و مشاوره تخصصی دریافت کنید. این سایت بهعنوان یکی از منابع معتبر در زمینه تجهیزات بستهبندی و خطوط تولید، اطلاعات بهروز و کاملی درباره جدیدترین مدلهای تیوب پرکن ارائه میدهد.
با خرید دستگاه تیوب پرکن تماماتومات از ارکان فلز، میتوانید تولید خود را با سرعت و دقت بالا انجام داده و هزینههای پرسنلی و خطاهای انسانی را به حداقل برسانید. همچنین تیم پشتیبانی فنی این مجموعه آماده ارائه خدمات نصب، راهاندازی و آموزش کار با دستگاه است.
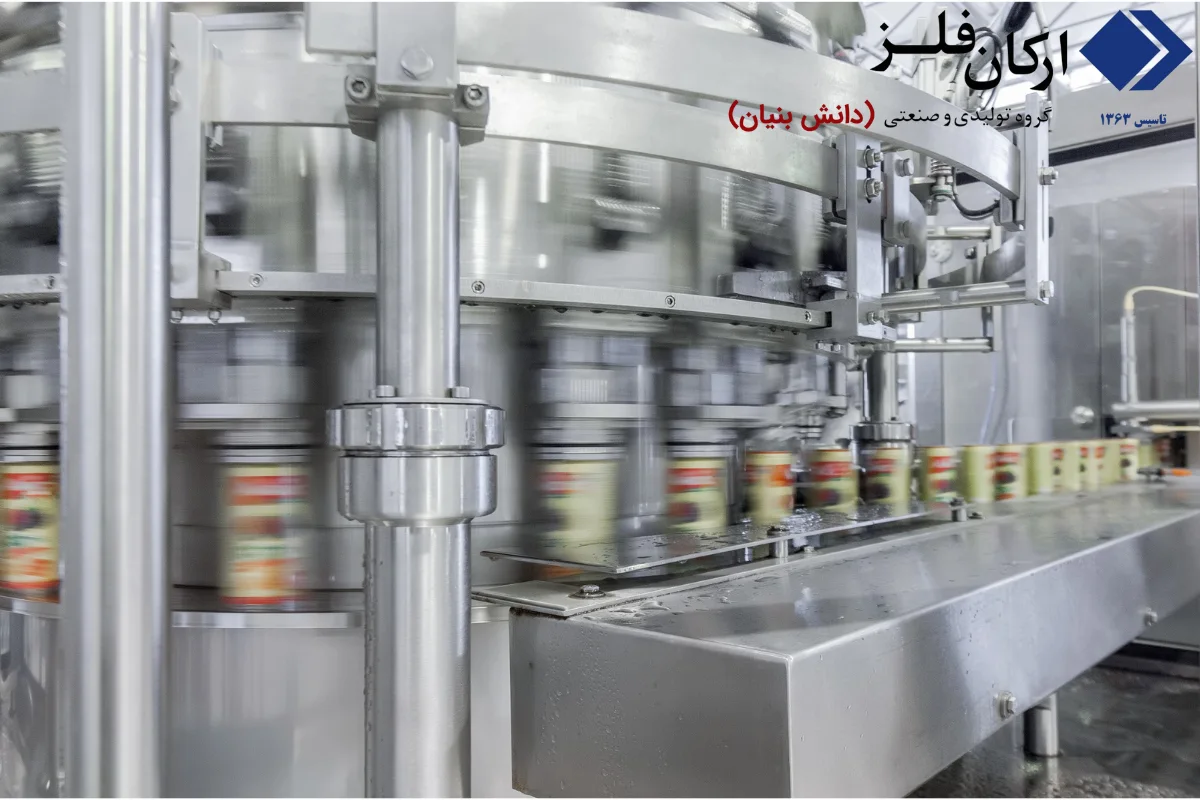
تفاوت تیوبهای لمینیت با سایر تیوبهای بستهبندی
تیوبهای لمینیت نسل جدیدی از بستهبندیهای انعطافپذیر هستند که با استفاده از چند لایه مواد پلیمری و آلومینیوم طراحی میشوند. این تیوبها به دلیل ساختار خاص خود، مقاومت بالایی در برابر نفوذ هوا، رطوبت و نور دارند و برای محصولاتی که نیاز به محافظت بالا دارند بسیار مناسب هستند.
برخلاف تیوبهای پلاستیکی معمولی که تنها از یک نوع پلیمر ساخته میشوند، تیوبهای لمینیتی از ترکیب چند ماده تشکیل شدهاند و این موضوع به آنها قابلیتهایی مانند چاپپذیری بهتر، ظاهر زیباتر، انعطاف بالا و دوام بیشتر میدهد. به همین دلیل بسیاری از برندهای مطرح در حوزه آرایشی و دارویی، به استفاده از تیوبهای لمینیت روی آوردهاند.
همچنین در مقایسه با تیوبهای آلومینیومی که در برابر فشار تغییر شکل دائمی پیدا میکنند، تیوبهای لمینیت پس از استفاده به حالت اولیه بازمیگردند و تجربه بهتری را برای مصرفکننده رقم میزنند. از این نظر، بستهبندی با تیوب لمینیتی هم از لحاظ فنی و هم از نظر بازاریابی برتری دارد.
در سایت ارکان فلز میتوانید اطلاعات فنی و تخصصی درباره تیوبهای لمینیتی و سازگاری آنها با دستگاههای تیوب پرکن را مطالعه کنید. این سایت راهنمایی کاملی برای تولیدکنندگانی است که به دنبال انتخاب بهترین نوع تیوب برای محصول خود هستند.
معرفی تیوب پرکن تمام اتومات لمینیت
دستگاه تیوب پرکن تمام اتومات لمینیت یکی از پیشرفتهترین تجهیزات بستهبندی در صنایع دارویی، آرایشی و شیمیایی است. این دستگاه مخصوص پر کردن و سیل کردن تیوبهای لمینیتی طراحی شده و با بهرهگیری از سیستمهای هوشمند و کنترل دقیق، فرآیند پر کردن را با دقت بالا، بدون نشتی و با ظاهری کاملاً حرفهای انجام میدهد.
از مهمترین ویژگیهای این دستگاه میتوان به قابلیت تنظیم حجم دقیق، سرعت بالا در تولید، سیستم سیل حرارتی یا التراسونیک، چاپ تاریخ و شماره بچ روی بدنه تیوب و امکان کار با تیوبهایی با سایزهای مختلف اشاره کرد. همچنین این دستگاه دارای سیستم کنترل PLC و پنل لمسی برای تنظیمات آسان و دقیقتر است.
اگر قصد راهاندازی یا ارتقاء خط تولید خود را دارید، تیوب پرکن تمام اتومات لمینیت ارکان فلز انتخابی حرفهای و قابل اعتماد برای شما خواهد بود. این دستگاه به صورت کاملاً اتوماتیک عملیات پر کردن، بستن، برش، چاپ و خروج محصول را انجام میدهد و برای تیراژهای بالا بسیار مناسب است.
در سایت ارکان فلز میتوانید مشخصات فنی، تصاویر، ویدیوی عملکرد و قیمت روز انواع تیوب پرکنهای لمینیت را بررسی کرده و با کارشناسان فنی جهت انتخاب مناسبترین مدل مشورت نمایید. این مجموعه علاوه بر فروش دستگاه، خدمات مشاوره، نصب، آموزش و پشتیبانی پس از فروش را نیز با بالاترین کیفیت ارائه میدهد.
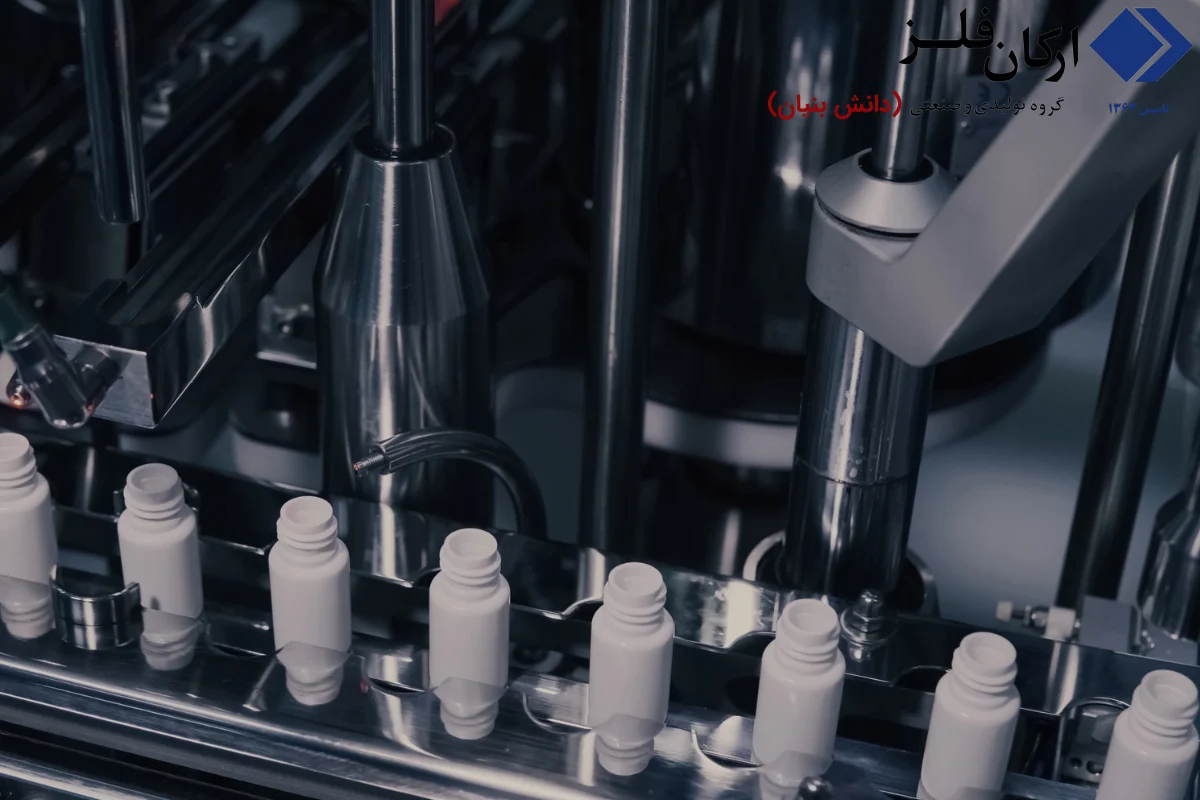
ساختار فنی دستگاه
دستگاه تیوب پرکن تمام اتومات لمینیت دارای ساختار فنی پیشرفته و صنعتی است که برای کار در خطوط تولید سنگین طراحی شده است. این دستگاه از بدنهای مقاوم و اجزای مکانیکی با دوام ساخته شده که اغلب از استنلس استیل 304 یا 316 تهیه میشوند. استفاده از استیل باعث میشود دستگاه در برابر خوردگی، زنگزدگی و واکنشهای شیمیایی مقاوم باشد و برای صنایع آرایشی، دارویی و غذایی مناسب گردد.
از نظر طراحی، ساختار فنی این دستگاه به گونهای است که قطعات بهراحتی قابل شستشو و نگهداری هستند. نواحی تماس با محصول کاملاً بهداشتی و قابل استریل بوده و طبق استانداردهای GMP طراحی شدهاند. اجزای اصلی آن شامل مخزن مواد، سیستم تزریق دقیق، مکانیزم درزگیری (سیل)، سیستم برش و بخشهای مکانیکی انتقال تیوبهاست. همچنین موتورهای استفادهشده در این دستگاه اغلب از برندهای مطرح هستند که موجب پایداری در عملکرد و کاهش خرابی میشود.
ارکان فلز با بررسی دقیق نیاز صنعتگران، مدلهایی از این دستگاه را ارائه میدهد که در عین حفظ کیفیت، قابلیت سفارشیسازی نیز دارند. مهندسی دقیق ساختار فنی دستگاه، باعث شده تا در مقایسه با مدلهای مشابه، بهرهوری بالاتری داشته باشد و نیاز به تعمیرات مکرر نداشته باشد. در سایت ارکان فلز، مشخصات فنی هر مدل بهصورت کامل درج شده و امکان مقایسه بین انواع مدلها نیز فراهم شده است تا انتخابی آگاهانه و فنی برای مشتریان انجام شود.
مکانیزم عملکرد
مکانیزم عملکرد دستگاه تیوب پرکن تمام اتومات لمینیت به گونهای طراحی شده که تمام مراحل پر کردن و بستهبندی تیوبها را بدون نیاز به دخالت دستی و با دقت بالا انجام میدهد. این فرآیند شامل چند مرحله اصلی است: تغذیه تیوب، تزریق ماده، درزگیری (سیل)، کدگذاری، برش و تخلیه نهایی روی نوار خروج.
در ابتدا، تیوبها از طریق بخش تغذیه خودکار در جایگاه مخصوص قرار میگیرند. سپس با دوز دقیق و کنترلشده، ماده مورد نظر از مخزن اصلی وارد هر تیوب میشود. این تزریق با تنظیم حجم دقیق انجام شده تا در مصرف مواد صرفهجویی شده و خروجی یکنواختی حاصل شود.
پس از پر شدن، تیوب وارد ایستگاه سیل میشود که معمولاً از سیستم حرارتی یا التراسونیک استفاده میکند. این بخش لبه تیوب را بهصورت محکم و استاندارد میبندد. بلافاصله بعد از آن، چاپگر صنعتی روی بدنه تیوب، تاریخ تولید، انقضا یا کد رهگیری را درج میکند. در نهایت، سر اضافی تیوب برش خورده و محصول نهایی از طریق نوار نقاله به مرحله بستهبندی منتقل میشود.
این مکانیزم اتوماتیک، سرعت تولید را بهطور چشمگیری افزایش داده و خطاهای انسانی را حذف میکند. در سایت ارکان فلز میتوانید ویدیوی کامل عملکرد این دستگاه را مشاهده کنید و با نحوه اجرای هر مرحله آشنا شوید. اگر به دنبال سیستمی هستید که عملکرد مداوم، دقیق و سریع ارائه دهد، این دستگاه بهترین انتخاب برای شماست.
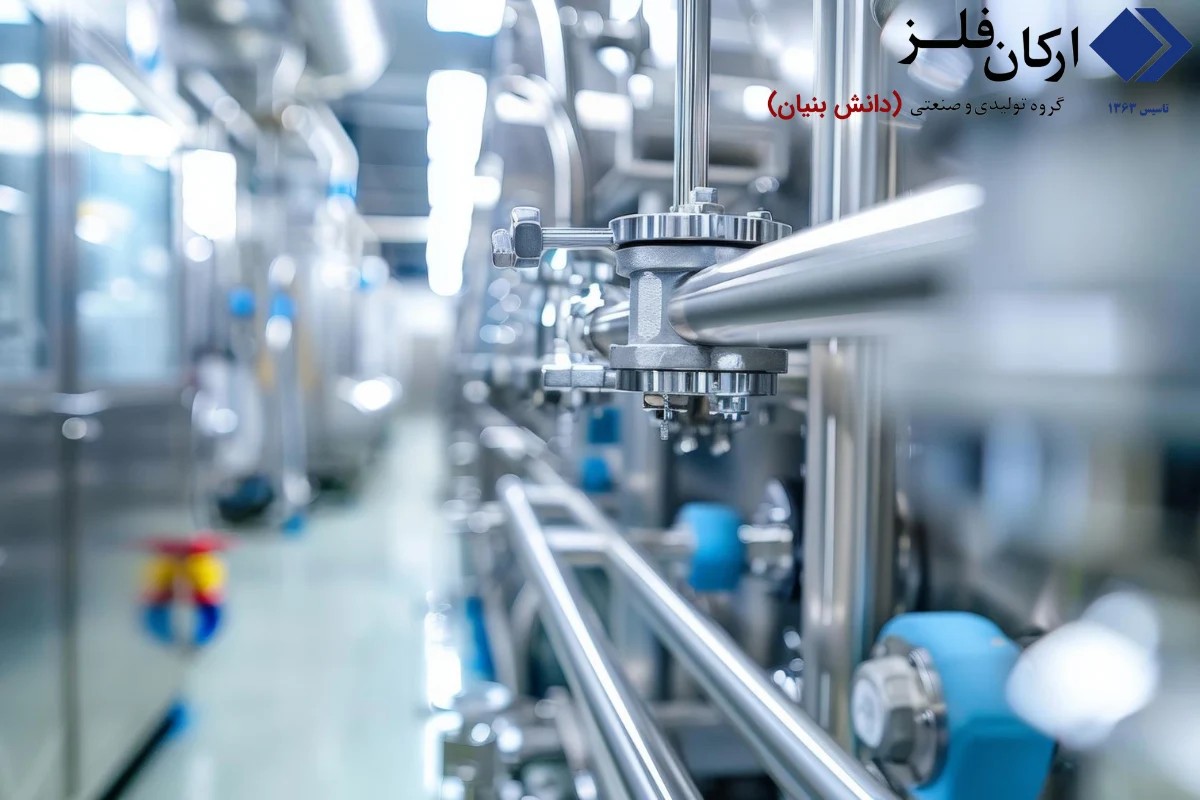
سیستم کنترل (PLC یا دیجیتال)
یکی از مهمترین بخشهای دستگاه تیوب پرکن تمام اتومات لمینیت، سیستم کنترل هوشمند آن است که معمولاً از نوع PLC صنعتی یا سیستم دیجیتال قابل برنامهریزی میباشد. این سیستمها وظیفه کنترل تمام مراحل دستگاه از جمله تزریق، سیل، برش، شمارش و توقف اضطراری را بر عهده دارند.
PLC (Programmable Logic Controller) یک کنترلر صنعتی قدرتمند و مقاوم در برابر نویزهای الکتریکی، ارتعاش و گرماست. این سیستم قابلیت تعریف دستورات دقیق، تنظیم حجم مواد، سرعت عملکرد، مدت زمان درزگیری و سایر پارامترها را دارد. اپراتور از طریق پنل لمسی HMI میتواند تمام بخشها را کنترل کرده و تنظیمات دلخواه را اعمال کند.
برتری دیگر سیستم کنترل PLC، قابلیت تشخیص خطا و هشدار سریع است. در صورت بروز هرگونه مشکل مانند عدم حضور تیوب، کمبود ماده، یا نقص در سیل، دستگاه بهصورت خودکار متوقف میشود و پیغام هشدار روی نمایشگر ظاهر میگردد.
در سایت ارکان فلز، مدلهایی از تیوب پرکن معرفی شدهاند که مجهز به جدیدترین سیستمهای PLC با برندهای مطرح مانند Siemens یا Delta هستند. این ویژگی باعث میشود دستگاه برای مدت طولانی بدون افت کیفیت و با عملکرد ثابت کار کند.
اگر به دنبال دستگاهی هستید که هم قابلاطمینان باشد و هم کنترل پیشرفتهای روی خط تولید داشته باشید، سیستم کنترل PLC یکی از فاکتورهای کلیدی در انتخاب شما خواهد بود. ارکان فلز با ارائه مشاوره فنی، شما را در این انتخاب همراهی میکند.
قابلیت برنامهریزی و ذخیرهی تنظیمات در تیوب پرکن
قابلیت برنامهریزی و ذخیرهی تنظیمات یکی از ویژگیهای بسیار کاربردی در دستگاه تیوب پرکن تمام اتومات لمینیت است که به تولیدکنندگان کمک میکند برای محصولات مختلف، تنظیمات خاصی را تعریف کرده و برای استفادههای بعدی ذخیره نمایند.
بهطور مثال، شما میتوانید برای هر تیوب خاص، حجم تزریق، زمان درزگیری، سرعت نوار نقاله و سایر پارامترها را یکبار تنظیم کرده و با یک کلیک برای سریهای بعدی مجدداً فراخوانی کنید. این موضوع باعث صرفهجویی در زمان، کاهش خطاهای اپراتور و افزایش دقت و یکنواختی تولید میشود.
این قابلیت معمولاً از طریق سیستم کنترل PLC و صفحه نمایش لمسی HMI در دسترس است. اپراتور میتواند پروفایلهای مختلفی تعریف کرده و هر بار تنها با انتخاب نام محصول، دستگاه را به صورت خودکار روی تنظیمات آن ست کند. برای خطوط تولیدی که تنوع محصول بالا دارند، این ویژگی حیاتی است.
در سایت ارکان فلز، مدلهایی از تیوب پرکن معرفی شدهاند که تا ۵۰ پروفایل مختلف را میتوانند ذخیره کنند و حتی قابلیت انتقال داده از طریق USB یا اتصال به شبکه را نیز دارند.
قابلیت ذخیره تنظیمات در کنار دقت و سرعت، تیوب پرکن تمام اتومات لمینیت ارکان فلز را به انتخابی هوشمندانه برای کارخانهها و کارگاههای حرفهای تبدیل کرده است.

اجزای اصلی دستگاه تیوب پرکن تمام اتومات لمینیت
دستگاه تیوب پرکن تمام اتومات لمینیت از مجموعهای از واحدهای دقیق و هماهنگ تشکیل شده که هرکدام نقش مهمی در فرآیند بستهبندی سریع و بدون خطا ایفا میکنند. این دستگاهها معمولاً برای پر کردن تیوبهای لمینیتی با محصولات نیمهمایع مانند کرم، ژل، پماد و خمیر دندان در خطوط تولید حرفهای استفاده میشوند. در ادامه اجزای اصلی این دستگاه را بررسی میکنیم.
واحد تغذیه تیوب
اولین مرحله در عملکرد دستگاه، تغذیه خودکار تیوبهای خالی است. این واحد تیوبها را از مخزن یا منبع ذخیره، یکییکی به بخش پرکن هدایت میکند. سیستم تغذیه بهگونهای طراحی شده که از گیر کردن یا ورود نادرست تیوب جلوگیری میشود. در مدلهای معرفیشده در سایت ارکان فلز، این بخش با سنسورهای هوشمند و بازوی مکانیکی دقیق تجهیز شده است.
سیستم پرکن
این واحد قلب اصلی دستگاه است. سیستم پرکن مواد نیمهمایع را با حجم تنظیمشده و یکنواخت درون تیوب تزریق میکند. دقت بالا در تزریق، کاهش ضایعات و یکنواختی حجم در هر تیوب از ویژگیهای مهم این بخش است. برخی مدلها دارای نازلهای ضدچکه و قابلیت تنظیم دمای مواد هستند.
واحد سیل حرارتی
پس از پر شدن، تیوب وارد بخش سیل میشود. این قسمت با استفاده از گرمای کنترلشده لبه تیوب را جوش میدهد. در تیوبهای لمینیتی، سیل باید بدون آسیب به لایهها و کاملاً محکم باشد. دستگاههای موجود در ارکان فلز دارای سیستمهای سیل حرارتی دقیق و قابل تنظیم هستند که کیفیت بستهبندی را تضمین میکنند.
سیستم چاپ کد تاریخ
این بخش تاریخ تولید، انقضا، یا شماره بچ را بهصورت مستقیم روی تیوب چاپ میکند. این سیستم معمولاً از چاپگرهای حرارتی یا جوهرافشان استفاده میکند و باید با سرعت بالای دستگاه هماهنگ باشد. کیفیت چاپ بالا و امکان تنظیم قالب چاپ از ویژگیهای مهم این قسمت است.
واحد برش و تخلیه
در مرحله پایانی، تیوبهای سیلشده توسط واحد برش، قسمتهای اضافی سر آنها جدا میشود و سپس روی نوار تخلیه یا میز جمعآوری قرار میگیرند. تخلیه منظم و بدون آسیب به تیوبها اهمیت زیادی دارد. برای مشاهده جزئیات فنی این اجزا و دریافت مشاوره تخصصی، به سایت ارکان فلز مراجعه کنید.
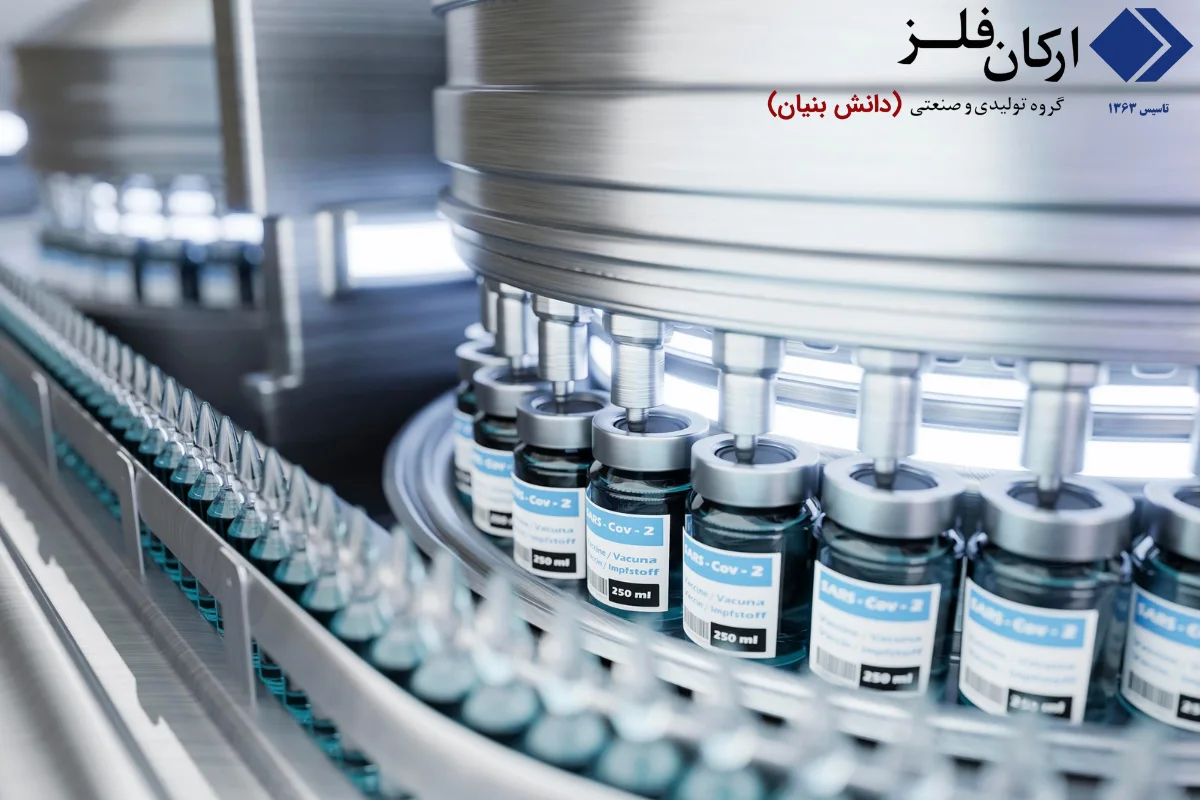
مزایای استفاده از دستگاه تیوب پرکن تمام اتومات لمینیت
استفاده از دستگاه تیوب پرکن تمام اتومات لمینیت در صنایع آرایشی، دارویی و شیمیایی، تحولی اساسی در روند بستهبندی محصولات ایجاد کرده است. این دستگاهها با بهرهگیری از فناوریهای روز، سرعت، دقت و یکنواختی در بستهبندی را افزایش میدهند و هزینههای تولید را به شکل محسوسی کاهش میدهند. در ادامه مهمترین مزایای این دستگاهها را بررسی میکنیم.
افزایش دقت و سرعت تولید
یکی از اصلیترین مزایای دستگاه تیوب پرکن تمام اتومات لمینیت، افزایش چشمگیر سرعت تولید است. این دستگاهها قادرند در هر دقیقه دهها تیوب را با دقت بالا پر کرده، سیل کنند و آماده بستهبندی نهایی نمایند. روند اتوماتیک و بدون توقف باعث میشود در مقایسه با سیستمهای دستی یا نیمهاتومات، ظرفیت تولید چند برابر شود.
همچنین دقت پر کردن در این دستگاهها بسیار بالا بوده و انحراف در حجم پرشده کمتر از چند درصد است. در مدلهای معرفیشده در سایت ارکان فلز، دستگاهها مجهز به سیستمهای اندازهگیری پیشرفته هستند که ضمن افزایش بهرهوری، ضایعات را نیز کاهش میدهند. این ویژگی بهویژه در تولید انبوه اهمیت زیادی دارد.
کاهش دخالت نیروی انسانی
یکی دیگر از مزایای مهم استفاده از این دستگاه، کاهش نیاز به نیروی انسانی در فرآیند بستهبندی است. در سیستمهای دستی یا سنتی، اپراتور باید تیوبها را پر کرده، سیل کند و آنها را مرتبسازی نماید که نهتنها زمانبر است، بلکه احتمال بروز خطا نیز بالاست.
اما دستگاه تیوب پرکن تمام اتومات لمینیت تمام مراحل را بهصورت خودکار انجام میدهد و تنها به یک اپراتور برای نظارت کلی نیاز دارد. این موضوع هم هزینههای نیروی کار را کاهش میدهد و هم ریسک آلودگی محصول و خطای انسانی را به حداقل میرساند. دستگاههای ارائهشده در سایت ارکان فلز دارای رابط کاربری سادهای هستند که اپراتور میتواند بدون تخصص بالا با آنها کار کند.
یکنواختی در حجم پرشده
یکی از دغدغههای اصلی تولیدکنندگان، حفظ یکنواختی در حجم مواد تزریقشده در هر تیوب است. عدم دقت در پر کردن، هم باعث نارضایتی مشتری میشود و هم میتواند منجر به زیان مالی برای تولیدکننده گردد.
دستگاه تیوب پرکن تمام اتومات با بهرهگیری از نازلهای دقیق و سیستم دوزینگ هوشمند، این مشکل را بهطور کامل برطرف میکند. در هر تیوب، مقدار مشخص و یکسانی از محصول تزریق میشود، بدون اینکه نوسانی در مقدار مشاهده شود. این ویژگی بهویژه در محصولات دارویی یا مراقبتی اهمیت بالایی دارد که دوز دقیق بسیار مهم است.
در سایت ارکان فلز، مدلهایی از این دستگاهها معرفی شدهاند که حتی قابلیت تنظیم حجم برای هر نوع تیوب را بهصورت ذخیرهشده دارند و این به تولیدکنندگان اجازه میدهد چند محصول را با یک دستگاه تولید کنند.
بهبود ظاهری محصول نهایی
ظاهر بستهبندی در بازار رقابتی امروز نقش تعیینکنندهای در جذب مشتری دارد. دستگاه تیوب پرکن تمام اتومات لمینیت با اجرای دقیق عملیات پر کردن، سیل، برش و چاپ، بستهبندیهایی با ظاهر حرفهای و استاندارد تولید میکند.
سیل یکنواخت و بدون نشتی، برش دقیق سر تیوب، چاپ تمیز تاریخ تولید و چیدمان مرتب تیوبها روی نوار خروجی، همگی موجب افزایش کیفیت ظاهری محصول میشوند. این امر باعث افزایش ارزش برند و اعتماد بیشتر مشتریان خواهد شد.
مدلهای موجود در ارکان فلز با استفاده از تجهیزات دقیق و فناوریهای روز، بستهبندیهایی با جلوه ظاهری بسیار مطلوب ارائه میدهند. برای تولیدکنندگانی که به جزئیات اهمیت میدهند و ظاهر محصول برایشان اهمیت دارد، این دستگاهها یک انتخاب ایدهآل هستند.
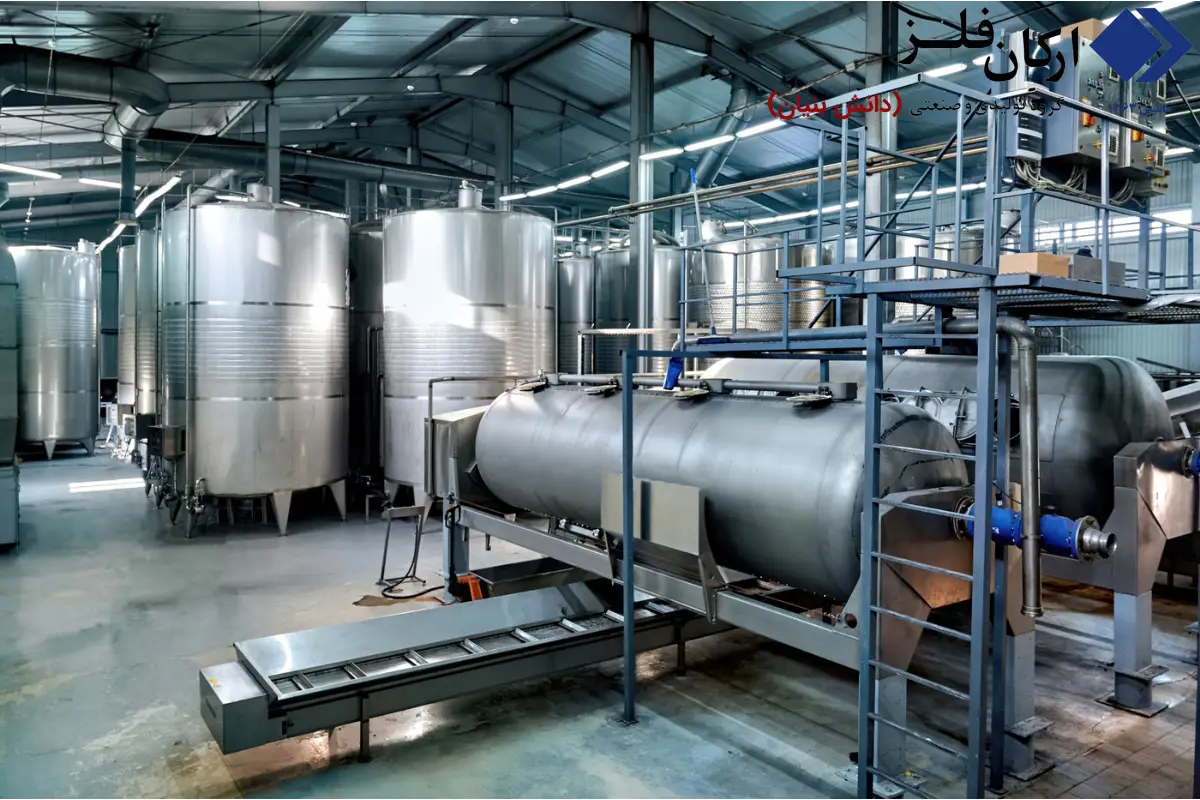
کاربردهای دستگاه تیوب پرکن تمام اتومات در صنایع مختلف
دستگاه تیوب پرکن تمام اتومات لمینیت، به دلیل طراحی پیشرفته و عملکرد دقیق، در صنایع مختلف کاربرد گستردهای دارد. این دستگاه با قابلیت پر کردن تیوبهای لمینیتی بهصورت سریع، بهداشتی و با دوز دقیق، برای بستهبندی محصولاتی که نیاز به بستهبندی بهداشتی و مصرف آسان دارند، ایدهآل است. در ادامه به کاربردهای این دستگاه در چهار صنعت مهم اشاره میکنیم.
صنعت آرایشی و بهداشتی (کرم، ژل، لوسیون)
یکی از اصلیترین کاربردهای دستگاه تیوب پرکن تمام اتومات، در صنعت تولید محصولات آرایشی و بهداشتی است. بسیاری از محصولات مانند کرمهای مرطوبکننده، ضدآفتاب، ژلهای حالتدهنده مو، ماسک صورت، سرم پوستی و لوسیونها، در تیوبهای لمینیتی عرضه میشوند.
این نوع بستهبندی علاوه بر زیبایی، امکان مصرف راحت، محافظت در برابر آلودگی و حمل آسان را فراهم میکند. دستگاههای ارائهشده در سایت ارکان فلز قادرند این نوع مواد را با دقت بالا و بدون آسیب به بافت آنها درون تیوبها تزریق کنند. سیستم سیل حرارتی باعث میشود درب تیوب کاملاً ایمن و بدون نشتی بسته شود.
صنایع دارویی (پماد، ژل درمانی)
در صنایع دارویی، رعایت استانداردهای بهداشتی، دوز دقیق و جلوگیری از آلودگی اهمیت ویژهای دارد. دستگاه تیوب پرکن تمام اتومات لمینیت در بستهبندی محصولاتی مانند پمادهای پوستی، ژلهای ضد درد، کرمهای آنتیبیوتیک، پماد چشمی یا ژلهای موضعی کاربرد گستردهای دارد.
این دستگاهها معمولاً از جنس استیل ضدزنگ با قطعات قابل استریل ساخته میشوند تا از رعایت کامل بهداشت در فرآیند تولید اطمینان حاصل شود. تنظیم دقیق حجم تزریق، استفاده از نازل ضدچکه و امکان کدگذاری تاریخ تولید، از مزایای این دستگاه برای داروسازان است.
در سایت ارکان فلز، مدلهایی با استاندارد GMP و مناسب برای استفاده در محیطهای دارویی معرفی شدهاند که نیازهای این صنعت را بهخوبی پاسخ میدهند.
صنایع غذایی (سس، خمیر شکلات)
در صنایع غذایی نیز از دستگاه تیوب پرکن برای بستهبندی موادی که بافت نیمهمایع دارند استفاده میشود. محصولاتی مانند سس گوجهفرنگی، سس خردل، مایونز، خمیر شکلات، کارامل یا حتی عسل، با استفاده از این دستگاه بهصورت کاملاً بهداشتی در تیوبهای مقاوم و قابل حمل بستهبندی میشوند.
مزیت استفاده از تیوب در این محصولات، حفظ بهداشت، جلوگیری از آلودگی و مصرف آسان برای مشتریان است. دستگاههای تیوب پرکن تمام اتومات لمینیت، امکان استفاده از نازلهای قابل شستوشو، بدنه ضدزنگ و سیل بهداشتی را دارند.
ارکان فلز دستگاههایی را ارائه میدهد که دارای مخازن گرمکننده و همزندار هستند؛ این ویژگی برای محصولاتی که به حفظ دما یا مخلوط شدن پیوسته نیاز دارند، بسیار مهم است.
صنایع شیمیایی (چسب، رنگ مو)
در صنایع شیمیایی، محصولات نیمهمایعی مانند چسبهای صنعتی، چسب فوری، رنگ مو، واکس، خمیر پولیش یا روانکنندهها در بستهبندی تیوبی بسیار رایج هستند. تیوبها علاوه بر جلوگیری از تبخیر یا تماس مستقیم با مواد، استفاده و نگهداری آسانی برای مصرفکننده دارند.
دستگاه تیوب پرکن تمام اتومات لمینیت میتواند این مواد را با دقت بالا در تیوب تزریق کرده و با سیل حرارتی کاملاً ایمن بستهبندی کند. در این صنعت، مقاومت تیوبها و سیستم سیل دستگاه باید بسیار قوی باشد تا از نشتی یا واکنش شیمیایی جلوگیری شود.
دستگاههای موجود در سایت ارکان فلز با قابلیت تنظیم ویسکوزیته ماده و مقاومت بالا در برابر مواد شیمیایی طراحی شدهاند. همچنین امکان افزودن سیستم تخلیه بدون هوا یا وکیوم نیز در برخی مدلها فراهم است.
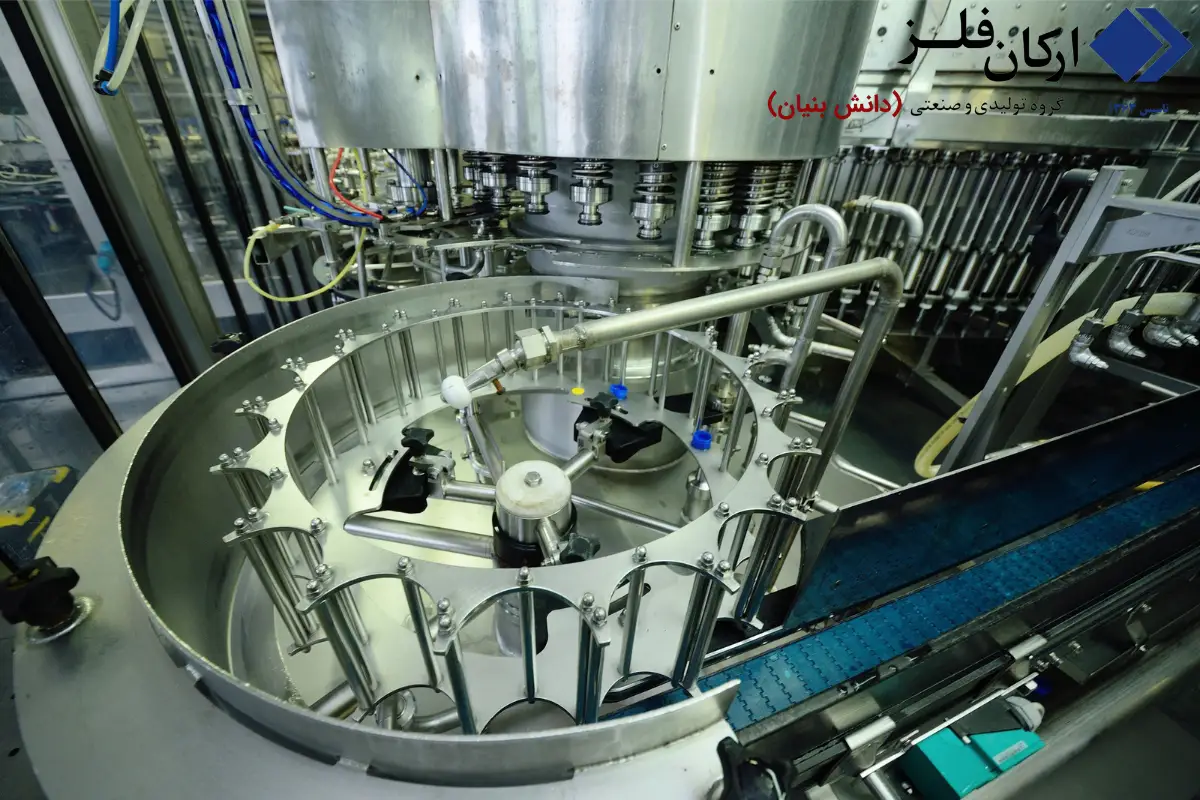
نکات کلیدی در انتخاب دستگاه تیوب پرکن لمینیت مناسب
انتخاب یک دستگاه تیوب پرکن لمینیت مناسب، تصمیمی حیاتی برای هر خط تولید آرایشی، دارویی، شیمیایی یا غذایی است. دستگاهی که انتخاب میشود باید با نوع محصول، ظرفیت تولید، تیوب مورد استفاده و شرایط محیطی هماهنگ باشد. با توجه به تنوع مدلها و مشخصات فنی، شناخت معیارهای اصلی برای خرید، به شما کمک میکند سرمایهگذاری هوشمندانهتری داشته باشید. در ادامه مهمترین نکاتی که باید هنگام خرید این دستگاه در نظر بگیرید را بررسی میکنیم.
حجم تولید موردنظر
نخستین قدم در انتخاب دستگاه تیوب پرکن، تعیین حجم تولید روزانه یا ماهانه شماست. اگر در مرحله تولید آزمایشی یا نیمهصنعتی هستید، دستگاههای با ظرفیت پایین و نیمهاتومات میتوانند پاسخگوی نیاز شما باشند. اما در تولید انبوه، بدون شک باید از دستگاههای تمام اتومات لمینیت استفاده کنید که قابلیت پر کردن صدها یا هزاران تیوب در ساعت را دارند.
مدلهای اتوماتیک با سیستمهای روتاری یا خطی، سرعت بالایی داشته و برای کارخانههایی با چندین شیفت کاری مناسباند. در سایت ارکان فلز، مدلهای مختلف بر اساس ظرفیت تولید دستهبندی شدهاند تا راحتتر بتوانید انتخاب خود را انجام دهید.
ابعاد و نوع تیوب
یکی از عوامل کلیدی در انتخاب دستگاه، سایز و جنس تیوبهایی است که در خط تولید استفاده میکنید. تیوبهای لمینیتی در ابعاد مختلف و با دهانههای متنوعی تولید میشوند. بنابراین باید دستگاهی را انتخاب کنید که بتواند با اندازههای مختلف تیوب سازگار باشد.
برخی مدلها تنها با تیوبهای استوانهای یا با قطر خاصی هماهنگ هستند، در حالی که مدلهای پیشرفتهتر امکان کار با تیوبهایی از جنس لمینیت، پلاستیک یا حتی آلومینیوم را نیز دارند. در سایت ارکان فلز، مشخصات فنی هر دستگاه شامل حداقل و حداکثر قطر تیوب قابل پشتیبانی بهصورت دقیق ذکر شده است.
قابلیت تطبیق با چند نوع ماده
اگر شما محصولاتی با ویسکوزیته یا چگالی متفاوت تولید میکنید (مثلاً کرم، ژل، چسب یا سس)، لازم است دستگاه شما توانایی تزریق دقیق در مواد مختلف را داشته باشد. مواد غلیظ نیاز به پمپهای قویتر و نازلهای مخصوص دارند، در حالیکه مواد روانتر ممکن است نیاز به کنترل دقیقتری برای جلوگیری از نشت داشته باشند.
برخی دستگاههای تیوب پرکن قابلیت تنظیم فشار، دما و سرعت تزریق را دارند و برای کارخانههایی که چند نوع ماده با خواص متفاوت تولید میکنند، بسیار کاربردی هستند. در ارکان فلز، مدلهایی معرفی شدهاند که دارای سیستمهای پرکن متغیر برای تنظیم ویسکوزیته ماده هستند.
توانایی تغییر سریع قالب
در خطوط تولیدی که تنوع محصول زیاد است، یکی از مهمترین ویژگیهای دستگاه تیوب پرکن، قابلیت تعویض سریع قالب است. این موضوع به اپراتور امکان میدهد بدون نیاز به توقف طولانی خط تولید، بین تیوبهایی با سایز یا دهانه متفاوت، تغییر انجام دهد.
دستگاههایی که مکانیزم تغییر قالب سادهتری دارند، در زمان و هزینه صرفهجویی میکنند. همچنین در مدلهای پیشرفته، تغییر تنظیمات از طریق پنل دیجیتال انجام میشود و حتی میتوان پروفایلهای مختلف را ذخیره کرد. در سایت ارکان فلز، مدلهایی با قابلیت تغییر سریع قالب معرفی شدهاند که برای کارخانههایی با تنوع محصول بالا، گزینهای ایدهآل محسوب میشوند.
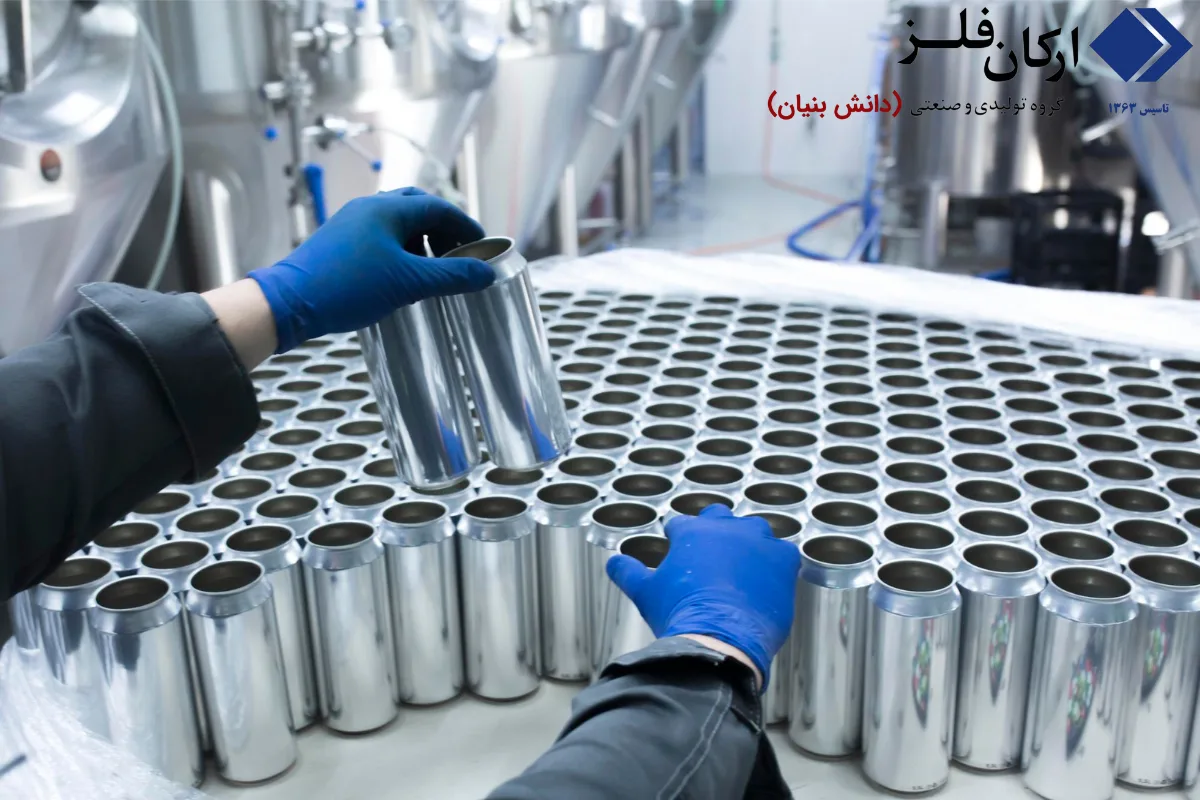
مقایسه دستگاههای نیمهاتومات و تماماتومات تیوب پرکن
دستگاههای تیوب پرکن به دو دسته اصلی نیمهاتومات و تماماتومات تقسیم میشوند که هرکدام مزایا و کاربردهای خاص خود را دارند. دستگاههای نیمهاتومات معمولاً برای تولید با حجم پایینتر و نیاز کمتر به سرعت بالا مناسب هستند. در این مدلها، برخی مراحل مانند قرار دادن تیوبها یا کنترل فرآیند نیاز به دخالت اپراتور دارد. به همین دلیل هزینه اولیه کمتر و نگهداری آسانتر است.
در مقابل دستگاههای تیوب پرکن تمام اتومات لمینیت قابلیت تولید با سرعت بسیار بالا، دقت بیشتر در حجم پرشده و کاهش خطای انسانی را دارند. این دستگاهها برای تولید انبوه و خطوط صنعتی بهینه هستند و در سایت ارکان فلز مدلهایی با تکنولوژی پیشرفته و سیستم کنترل دیجیتال عرضه میشوند.
اگرچه هزینه اولیه دستگاه تمام اتومات بیشتر است، اما در طولانیمدت با افزایش بهرهوری و کاهش نیروی انسانی، صرفهجویی چشمگیری در هزینهها ایجاد میشود. انتخاب بین این دو نوع دستگاه بستگی به نیاز تولید، بودجه و حجم سفارشات شما دارد.
چالشها و راهکارهای عملی در استفاده از تیوب پرکن تمام اتومات
استفاده از دستگاههای تیوب پرکن تمام اتومات لمینیت با مزایای فراوانی همراه است اما چالشهایی نیز دارد که شناخت و رفع آنها برای حفظ کیفیت تولید ضروری است. یکی از چالشهای رایج، تنظیم دقیق حجم پرکردن تیوب است که در صورت عدم تنظیم صحیح میتواند منجر به نشت یا پر شدن ناقص شود.
راهکار عملی برای این موضوع، استفاده از سیستم کنترل دیجیتال و برنامهریزی دقیق تنظیمات دستگاه است که در مدلهای پیشرفته سایت ارکان فلز بهکار رفته است. همچنین تمیزکاری منظم نازلها و اجزای پرکن برای جلوگیری از گرفتگی اهمیت زیادی دارد.
چالش دیگر تنظیم سریع قالب برای انواع تیوبهای متفاوت است که باعث توقف طولانی خط تولید میشود. مدلهایی با سیستم تعویض سریع قالب که در ارکان فلز عرضه میشوند، این مشکل را کاهش دادهاند. در نهایت آموزش صحیح اپراتورها و انجام سرویس دورهای دستگاه از مهمترین راهکارها برای کاهش خطا و افزایش عمر مفید دستگاه است.
راهنمای نگهداری و سرویس دستگاه تیوب پرکن لمینیت
نگهداری منظم و سرویس دورهای دستگاه تیوب پرکن لمینیت نقش مهمی در افزایش عمر و حفظ کیفیت عملکرد آن دارد. اولین نکته، پاکسازی منظم قسمتهای تماس با ماده پرکن است تا از تجمع مواد خشکشده یا باقیمانده جلوگیری شود که میتواند باعث اختلال در عملکرد شود.
در دستگاههای موجود در سایت ارکان فلز، توصیه میشود هر روز پس از پایان کار، نازلها و مخازن بهطور کامل تمیز شوند. علاوه بر آن، بررسی و روغنکاری منظم قطعات مکانیکی مانند زنجیرها و بلبرینگها از خرابی زودرس جلوگیری میکند.
سیستمهای کنترل دیجیتال باید بهصورت دورهای بررسی و بهروزرسانی نرمافزاری شوند تا دقت و سرعت عملکرد حفظ شود. همچنین تنظیم مجدد سنسورها و قطعات برقی باید توسط تکنسینهای مجرب انجام شود.
رعایت نکات ایمنی در زمان سرویس و آموزش اپراتورها برای انجام مراقبتهای روزانه، از بروز خرابیهای ناگهانی جلوگیری میکند و بهرهوری دستگاه را در طولانیمدت تضمین مینماید.
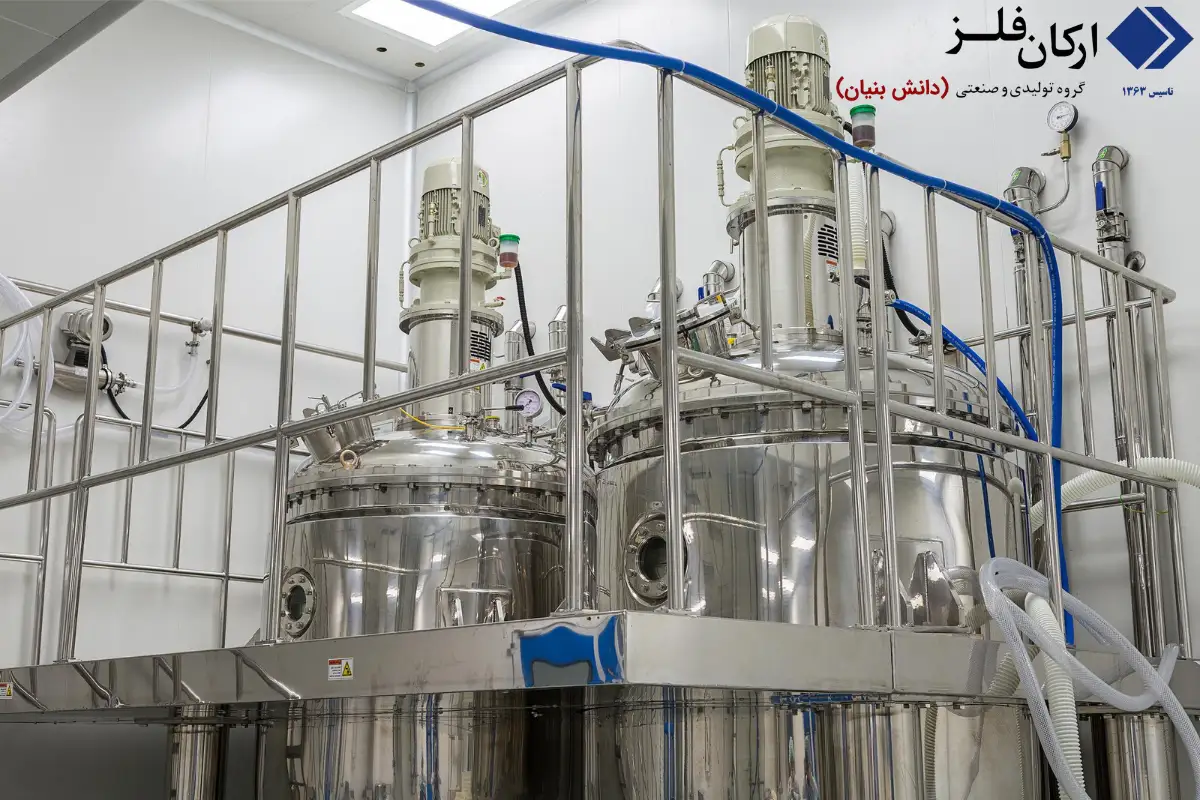
عوامل مؤثر بر قیمت دستگاه تیوب پرکن لمینیت تماماتومات
قیمت دستگاه تیوب پرکن لمینیت تماماتومات تحت تأثیر عوامل متعددی قرار دارد که شناخت آنها به شما کمک میکند بهترین انتخاب را متناسب با نیاز و بودجه خود داشته باشید. اولین عامل، ظرفیت تولید دستگاه است؛ دستگاههای با توان تولید بالا معمولاً قیمت بیشتری دارند.
عامل دیگر کیفیت قطعات و مواد استفاده شده در ساخت دستگاه است. دستگاههای دارای بدنه استیل ضدزنگ و قطعات مقاوم در برابر خوردگی که در سایت ارکان فلز عرضه میشوند، قیمت بالاتری دارند اما طول عمر بیشتری نیز دارند.
سیستم کنترل دستگاه مانند پنلهای دیجیتال پیشرفته، قابلیت برنامهریزی و اتصال به شبکههای اتوماسیون صنعتی نیز بر قیمت تأثیرگذار است. همچنین ویژگیهایی مانند تغییر سریع قالب، سیستم چاپ تاریخ، و نازلهای مخصوص برای انواع مواد مختلف باعث افزایش هزینه میشوند.
در نهایت خدمات پس از فروش و گارانتی نیز بخشی از قیمت کلی دستگاه است که نقش مهمی در انتخاب درست دارد. در سایت ارکان فلز میتوانید با بررسی کامل مشخصات و دریافت مشاوره، دستگاهی با بهترین قیمت و کیفیت را انتخاب کنید.
تحلیل بازدهی اقتصادی دستگاه در خطوط تولید پیوسته
استفاده از دستگاه تیوب پرکن تمام اتومات لمینیت در خطوط تولید پیوسته، بازدهی اقتصادی بالایی را برای تولیدکنندگان به همراه دارد. این دستگاهها با افزایش سرعت پرکردن تیوبها، کاهش خطاهای انسانی و به حداقل رساندن هدررفت مواد اولیه، هزینههای عملیاتی را به شکل چشمگیری کاهش میدهند. بهعلاوه، قابلیت تولید مداوم و بدون توقف، بهرهوری کل خط تولید را افزایش میدهد.
در خطوط تولید پیوسته، انتخاب دستگاهی با قابلیت تنظیم سریع و دقیق حجم پرشدن تیوب اهمیت دارد تا بتوان انواع محصولات را بدون نیاز به وقفه زیاد تولید کرد. دستگاههای پیشرفته موجود در سایت ارکان فلز با سیستمهای کنترل دیجیتال، این امکان را به تولیدکننده میدهند تا تنظیمات دستگاه را ذخیره و در صورت نیاز سریع بازیابی کنند.
سرمایهگذاری اولیه روی این دستگاهها شاید بالا به نظر برسد، اما با توجه به کاهش نیروی انسانی، افزایش کیفیت و سرعت تولید و کاهش ضایعات، بازگشت سرمایه به سرعت صورت میگیرد. بنابراین تحلیل دقیق بازدهی اقتصادی و تطابق دستگاه با نیازهای خط تولید، کلید موفقیت در انتخاب دستگاه مناسب است.
تکنولوژیهای روز در طراحی تیوب پرکنهای پیشرفته
صنعت بستهبندی تیوب، با استفاده از تکنولوژیهای نوین به سرعت در حال پیشرفت است. دستگاههای تیوب پرکن پیشرفته از فناوریهایی مانند سیستمهای کنترل PLC و HMI لمسی، موتورهای سروو با دقت بالا و حسگرهای اتوماتیک بهره میبرند که دقت و سرعت تولید را به طور چشمگیری افزایش میدهد.
در طراحی این دستگاهها، استفاده از قطعات با دوام و مقاوم در برابر خوردگی، مانند استیل ضدزنگ، سبب افزایش عمر دستگاه و کاهش هزینههای نگهداری میشود. همچنین قابلیت برنامهریزی و ذخیره پروفایلهای مختلف تولید، امکان تغییر سریع تنظیمات برای انواع تیوب و محصولات را فراهم میکند.
برخی از مدلهای تیوب پرکن تمام اتومات موجود در سایت ارکان فلز دارای سیستم چاپ تاریخ و کدگذاری اتوماتیک هستند که با استفاده از تکنولوژی جوهر افشان یا لیزر انجام میشود. این ویژگی برای رعایت استانداردهای کیفیت و ردگیری محصولات اهمیت زیادی دارد.
تکنولوژیهای نوین باعث شدهاند دستگاههای تیوب پرکن لمینیت، علاوه بر افزایش بهرهوری، از نظر کیفیت نهایی محصول نیز عملکردی بینظیر داشته باشند.
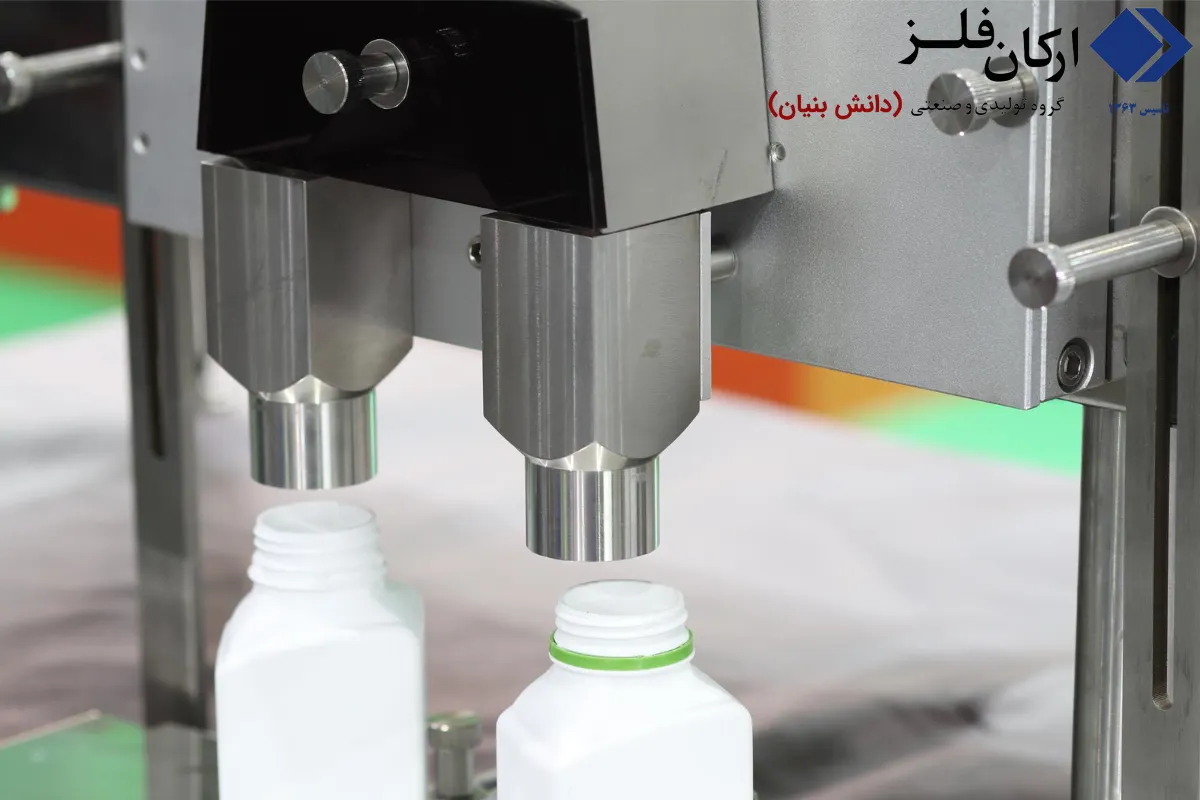
نمونهکارهای موفق از کاربرد دستگاه در برندهای معتبر
دستگاههای تیوب پرکن تمام اتومات لمینیت، در خطوط تولید برندهای معتبر جهانی و داخلی به عنوان یکی از کلیدهای موفقیت شناخته شدهاند. شرکتهایی که در صنایع آرایشی، دارویی، غذایی و شیمیایی فعالیت دارند، با استفاده از این دستگاهها توانستهاند سرعت تولید، کیفیت بستهبندی و رضایت مشتریان خود را به شکل قابل توجهی ارتقا دهند.
برای مثال، یکی از برندهای معروف آرایشی با استفاده از دستگاه تیوب پرکن تمام اتومات ارکان فلز، توانسته تولید روزانه خود را سه برابر کرده و خطاهای پرکردن را به کمتر از ۰.۵ درصد کاهش دهد. این موفقیت در افزایش کیفیت محصول و کاهش هزینههای تولید نقش مهمی داشته است.
نمونهکارهای موفق دیگری نیز در صنعت دارویی وجود دارد که استفاده از دستگاههای پیشرفته تیوب پرکن لمینیت منجر به بهبود دقیقیت دوز مواد و افزایش عمر مفید محصولات شده است. گزارشهای رضایت مشتریان و بازخورد مثبت در سایت ارکان فلز گواه این موفقیتها است.
جمعبندی:
چرا استفاده از تیوب پرکن تمام اتومات لمینیت یک انتخاب هوشمندانه برای تولیدکنندگان است
استفاده از دستگاه تیوب پرکن تمام اتومات لمینیت، یک انتخاب هوشمندانه و اقتصادی برای تولیدکنندگان در صنایع مختلف است. این دستگاهها با افزایش سرعت و دقت پرکردن، کاهش خطاهای انسانی و تضمین یکنواختی حجم مواد، کیفیت نهایی محصولات را به طور قابل توجهی بهبود میبخشند.
علاوه بر این دستگاههای پیشرفته موجود در سایت ارکان فلز، با طراحی مدرن و بهرهگیری از فناوریهای روز، قابلیت تطبیق با انواع تیوب و مواد مختلف را دارند که انعطافپذیری تولید را افزایش میدهد. کاهش هزینههای عملیاتی و افزایش بهرهوری، از دیگر مزایای مهم این دستگاهها است.
همچنین امکان تغییر سریع قالب و ذخیره تنظیمات در دستگاههای تمام اتومات، تولید چند محصول متفاوت را بدون نیاز به توقف طولانی خط تولید فراهم میکند. این ویژگیها دستگاه تیوب پرکن تمام اتومات لمینیت را به گزینهای ایدهآل برای تولیدکنندگان حرفهای تبدیل کرده است. با توجه به تمام این نکات، انتخاب دستگاه از سایت ارکان فلز، سرمایهگذاری هوشمندانهای برای افزایش کیفیت و کمیت تولید شما خواهد بود.
برای دریافت مشاوره کافیست با کارشناسان ما در ارتباط باشید یا با شماره های زیر تماس حاصل فرمایید.
02833857